Tool Steel
Tool Steel Product Guide
The term “tool steel” applies to a wide range of carbon and alloy steels that are often used in manufacturing various types of tools. Tool steel production is conducted on a significantly lower scale compared to steel used in consumer products. However, the implementation of stringent quality control processes guarantees that a specific grade of tool steel will be capable of carrying out some function like machining or perforating.
Also, tool steel is often used in the heat-treated condition. And due to the increased proportions of minerals such as vanadium and niobium that are included in several high-carbon tool steels, these steels also have greater corrosion resistance.
Table of Contents
Introduction
Tool steel, a metal alloy characterized by its toughness and heat resistance, is an essential material in the engineering world. Primarily containing tungsten, molybdenum, cobalt, and vanadium, this type of steel showcases excellent durability and heat resistance, making it an optimal choice for cutting and drilling operations. It is categorized into six groups based on its usage and specific properties: water-hardening, cold-work, shock-resisting, high-speed, hot-work, and special purpose. The selection depends on various factors, including cost-effectiveness, working temperature, surface hardness requirement, strength, shock resistance, and toughness. In instances where there are more demanding requirements, higher alloy content and carbides may be required.
The Intricacies of Tool Steel Composition
Tool steels carry an array of different elements to enhance their heat resistance and durability. The compositions and combinations vary depending on the specific class of the tool steel. Here is a general rundown:
Water-Hardening Class (W)
It gets its name from its primary property of needing to be water quenched. Essentially, it’s plain high carbon steel, widely used due to its affordability.
Cold-Work Classes (O, A, D)
This group consists of oil-hardening, air-hardening, and high carbon-chromium tool steels. They exhibit high hardenability, wear resistance, and average toughness. They’re usually involved in producing larger parts or parts demanding minimum distortion when hardened.
Shock-Resisting Class (S)
This class of steel has high shock resistance and good hardenability. It’s designed to withstand shock at both low and high temperatures. It also boasts high impact toughness and relatively low abrasion resistance.
Hot-Working Class (H)
Hot-work tool steels, H1-H59, were specifically engineered to maintain strength and hardness during prolonged exposure to elevated temperatures.
High-Speed Class (M, T)
Tungsten and Molybdenum-based tool steels are used for cutting tools when it is crucial to retain strength and hardness at high temperatures.
Plastic Mold and Special Purpose Classes (P, L, F)
The P-Code steels are designed for plastic injection molding dies, while L-Code tool steels are low alloy special purpose tool steels, and F-Code steels are Carbon/Tungsten-based.
Unraveling the Manufacturing Process of Tool Steel
Tool steel is produced through several sophisticated steps:
Electric Arc Furnace (EAF): The process starts with melting recycled steel scrap along with alloying components in an electric arc furnace. The molten mixture is combined with chemicals to prevent oxidation. The impurities are eliminated during the refining stage, and the steel flows into large molds to form ingots.
Electroslag Refining (ESR): This method involves progressive melting, producing high-grade steel with fewer imperfections.
Annealing: The steel is heated to a certain temperature, held there for a specified time, and then cooled down. This alters the molecular structure of the steel, making it less brittle and more workable.
Hot or Cold Drawing: To achieve higher tolerances, smaller sizes, or unique shapes, drawing processes are employed.
Practical Applications of Tool Steel
Due to its excellent properties, tool steel is utilized in a wide range of applications. It is widely employed for making:
- Cutting tools: drills, reamers, and machine dies
- Hand tools: screwdrivers, hammers, and chisels
- Molds: plastic injection molding
How to Choose the Right Tool Steel: Five Key Tips
1. Evaluate Your Requirements
Different tool steel types have different strengths and weaknesses. You must first understand the demands of your application before deciding on the type of tool steel to use.
2. Consider the Working Temperature
If your tool will operate at high temperatures, consider a hot-work or high-speed tool steel. For lower temperatures, cold-work or shock-resisting tool steel might be more suitable.
3. Assess the Toughness Requirement
If your tool is likely to experience shock or impact, opt for shock-resisting tool steel. For applications that require high wear resistance, a cold-work tool steel would be a better choice.
4. Don’t Ignore the Cost
Cost-effectiveness is crucial. While specialized tool steels may offer enhanced performance, they often come with a higher price tag. Consider whether the benefits justify the extra cost for your specific application.
5. Take Expert Advice
When in doubt, consult with an expert. They can help you understand your needs better and guide you to the best choice based on your application requirements.
Wrapping Up
Tool steels, with their unique properties, serve as the backbone of many industries. Their excellent heat resistance, toughness, and wear resistance make them a preferred choice for many applications, from drilling and cutting to molding and shearing. Understanding their classifications, compositions, and manufacturing processes can aid in selecting the best tool steel for your specific requirements.
Tool Steel Group | Tool Steel Symbol | Attribute |
---|---|---|
Water-Hardening | W | Water-hardening |
Cold-Worked | O | Oil-hardening |
Cold-Worked | A | Air-hardening |
Cold-Worked | D | High carbon, high chromium |
Hot-Worked | H | H40-H59 (molybdenum-based) |
Hot-Worked | H | H20-H39 (tungsten-based) |
Hot-Worked | H | H1-H19 (chromium-based) |
High-speed | M | Molybdenum-based |
High-speed | T | Tungsten-based |
Plastic Mold | P | Low-carbon, chromium and nickel-based |
Special Purpose | F | Carbon/tungsten based |
Special Purpose | L | Low alloy |
Request for Quotation
Request For Quote
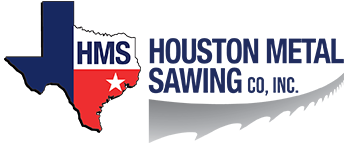
Monday through Friday
8:00 AM to 5:00 PM Central Time
Houston, Texas 77093
Precision Cutting Specialist
Our sawing capabilities include a large range of metals, castings, plastics or molded parts. You can count on Houston Metal Sawing to deliver your parts on time and within budget.
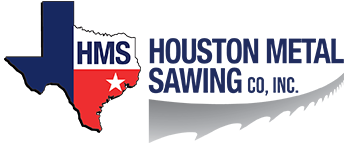