Stainless Steel
Stainless Steel Product Guide
As with other varieties of steel, stainless steel is made up of two or more different metals that have been alloyed together or “melted” into one. The metal iron, to which a marginal quantity of carbon has been added, is the primary “component” (the term used for the alloying element) that constitutes steel. This is something that is shared by all types of steel. Metal chromium (typically at least 11% by weight) was added to conventional steel in the early 20th century, which resulted in a bright, shining surface that was very resistant to corrosion. This was the beginning of stainless steel, which has been used ever since. However, stainless steel is unique among steels because of its corrosion resistance, a term we use to describe its ability to resist rust.
Table of Contents
Each type offers unique properties suited for specific environments and uses. Type 301 is known for its high strength and excellent corrosion resistance, making it ideal for dynamic environments. Type 303, with added sulfur, offers enhanced machinability. Type 304, the most common stainless steel, provides a good balance of corrosion resistance and strength, while Type 316, with added molybdenum, stands out in environments with high chloride exposure. This comparison aims to elucidate the distinct characteristics of each type to help in making informed decisions.
Property | 301 Stainless Steel | 303 Stainless Steel | 304 Stainless Steel | 316 Stainless Steel |
---|---|---|---|---|
Composition | 17% Chromium, 7% Nickel, 0.15% Carbon | 17% Chromium, 8% Nickel, 0.15% Carbon, added Sulfur | 18% Chromium, 8% Nickel, 0.08% Carbon | 16% Chromium, 10% Nickel, 2% Molybdenum, 0.08% Carbon |
Corrosion Resistance | High, particularly against environmental exposure | Good, especially in mildly corrosive environments | Excellent, versatile in various environments | Superior, especially in chloride environments |
Strength | High, with notable ductility | Moderate, with enhanced machinability | Balanced strength and ductility | High, especially in harsh environments |
Weldability | Good, but may require post-weld annealing | Fair, not typically chosen for welding | Excellent, versatile in welding applications | Excellent, with superior resistance to corrosion post-weld |
Machinability | Good, suitable for forming and drawing | Excellent, best among the four | Good, widely used for various applications | Good, similar to 304 but with better corrosion resistance |
Common Applications | Aerospace, automotive parts, kitchen utensils | Fasteners, fittings, gears, where smooth machining is needed | Food processing equipment, kitchenware, general applications | Marine environments, chemical processing, medical implants |
Cost | Moderate, varies with nickel content | Similar to 304, slightly higher due to added sulfur | Most cost-effective among the four | Higher, due to added molybdenum |
The T-304 stainless steel is commonly used in the world. It may be found in everything from automobiles and daggers to the Space Station. Another name for it is “food grade.” It can be welded and machined with strong corrosion resistance to various chemical corrodents and industrial atmospheres. Forms easily and may be easily welded using any of the most typical methods.
Finally, 304 high fatigue resistance makes it an excellent option for applications that will be subjected to stress or strain for an incredibly long time. So, it is extensively utilized in aircraft applications as a lightweight, strong, and durable material.
304 Stainless Steel (annealed condition) | ||||
---|---|---|---|---|
Minimum Properties | Ultimate Tensile Strength, ps | 73,200 | ||
Yield Strength, psi | 31,200 | |||
Elongation | 70% | |||
Rockwell Hardness | B70 | |||
Chemistry | Iron (Fe) | 66.5 – 74 | ||
Carbon (C) | 0.08% max | |||
Chromium (Cr) | 18 – 20% | |||
Manganese (Mn) | 2% max | |||
Nickel (Ni) | 8 – 10.5% | |||
Phosphorus (P) | 0.045% max | |||
Sulphur (S) | 0.03% max | |||
Silicon (Si) | 1% max |
316 Stainless Steel
316 stainless steel boasts an enhanced resistance against corrosion and pitting, offering a more robust protection than its counterpart, T304 stainless steel. Beyond just its resistance, it also has a commendable thermal strength that outperforms the T304 type.
It’s extensively used in the pulp and paper industry, and it plays a pivotal role in the manufacturing of pumps. The maritime sector, given the need for corrosion-resistant materials, also utilizes this steel in producing essential equipment. Additionally, valves that require strength and resistance often employ 316 stainless steel. T-316 is machinable and weldable like T-304, but it is more resistant to corrosion.
316 stainless steel (annealed condition) | ||||
---|---|---|---|---|
Minimum Properties | Ultimate Tensile Strength, ps | 89,900 | ||
Yield Strength, psi | 60,200 | |||
Elongation | 45% | |||
Rockwell Hardness | B91 | |||
Chemistry | Iron (Fe) | 65% | ||
Carbon (C) | 0.08% max | |||
Chromium (Cr) | 17% | |||
Manganese (Mn) | 2% | |||
Molybdenum (Mo) | 2.5% | |||
Nickel (Ni) | 12% | |||
Phosphorus (P) | 0.045% | |||
Sulphur (S) | 0.03% min | |||
Silicon (Si) | 1% |
303 Stainless Steel
Tensile strength of 303 stainless steel typically ranges from 500 to 750 MPa, depending on various factors including heat treatment and processing methods. It’s crucial to note that while 303 stainless steel has good machinability properties, its tensile strength is slightly lower than that of other stainless steel grades.
T-303 is a version of T-302/304 that allows for free machining and may be used in automated machining processes. It is one of the three primary alloys of stainless steel that are commercially accessible. The key rationale for using 303 is when you want stainless steel with superior machining capabilities than 304 and 316. Although it has a similar level of corrosion resistance as 304, its performance falls short of 316. However, the real downside of the alloy is that it is not widely accepted as being weldable.
303 stainless steel rockwell hardness typically ranges between 95-110 HRB (Rockwell B Hardness Scale). This grade is known for its machinability and non-magnetic properties.
For optimal machining of 303 stainless steel speeds and feeds, recommended spindle speeds are between 60-80 RPM for drilling and 60-90 RPM for milling, with feed rates from 0.002 to 0.006 inches per revolution in drilling.
303 stainless steel (cold drawn annealed, room temperature) | ||||
---|---|---|---|---|
Minimum Properties | Ultimate Tensile Strength, ps | 89,900 | ||
Yield Strength, psi | 34,800 | |||
Elongation | 50% | |||
Rockwell Hardness | B83 | |||
Chemistry | Iron (Fe) | 69% | ||
Carbon (C) | 0.15% max | |||
Chromium (Cr) | 18% | |||
Manganese (Mn) | 2% max | |||
Molybdenum (Mo) | 0.6% max | |||
Nickel (Ni) | 9% | |||
Phosphorus (P) | 0.2% max | |||
Sulphur (S) | 0.15% min | |||
Silicon (Si) | 1% max |
301 Stainless Steel
301 stainless steel 1/4 hard properties are known for their unique balance of ductility and strength. This specific temper exhibits good corrosion resistance, excellent formability. It’s often chosen for components that require moderate wear resistance and robust performance, bridging the gap between softer tempers and full hardness variations. In essence, the 1/4 hard condition is a versatile choice in the 301 stainless steel range.
It is possible to provide Grade 301 in ribbon and wire shapes with a tensile strength of up to 1800 MPa, allowing tempers ranging from 1/16 hard to full hardness. It is possible to roll or break Grade 301 into an airplane, structural, and notably train car components because of its regulated analysis. On the other hand, 3/4 to complete hard tempers must be used if parts of basic form designs call for exceptional wear resistance and spring characteristics.
However, there are two grades of 301L, one with low carbon content and the other 301LN with greater nitrogen content. The latter has a more incredible work-hardening pace than the former.
301 stainless steel | ||||
---|---|---|---|---|
Minimum Properties | Ultimate Tensile Strength, ps | 74,700 min | ||
Yield Strength, psi | 29,700 min | |||
Elongation | 40% min | |||
Rockwell Hardness | B85 | |||
Minimum Properties (1/4 hard condition) | Ultimate Tensile Strength, psi | 125,000 m | ||
Yield Strength, psi | 75,000 mi | |||
Elongation | 25% min | |||
Rockwell Hardness | C25 | |||
Minimum Properties (1/2 hard condition) | Ultimate Tensile Strength, ps | 150,000 min | ||
Yield Strength, psi | 110,000 | |||
Elongation | 18% min | |||
Rockwell Hardness | C32 | |||
Minimum Properties (3/4 hard condition) | Ultimate Tensile Strength, ps | 185,000 min | ||
Yield Strength, psi | 140,000 min | |||
Elongation | 9% min | |||
Rockwell Hardness | C41 | |||
Chemistry | Iron (Fe) | 69% | ||
Carbon (C) | 0.15% max | |||
Chromium (Cr) | 18% | |||
Manganese (Mn) | 2% max | |||
Molybdenum (Mo) | 0.6% max | |||
Nickel (Ni) | 9% | |||
Phosphorus (P) | 0.2% max | |||
Sulphur (S) | 0.15% min | |||
Silicon (Si) | 1% max |
302 Stainless Steel
Carbon content in type 302 is somewhat more significant than in type 304, which is why it is most often encountered in strip and wire form. However, 304 and 304L are increasingly employed in many sectors because of advancements in melting techniques, availability, and affordability. It is applicable for spinning, wire formation, and stamping. This, of course, makes the alloy formed into all sorts of cables, washers, screens, and springs.
302 Stainless Steel (annealed condition) | ||||
---|---|---|---|---|
Minimum Properties | Ultimate Tensile Strength, ps | 89,900 | ||
Yield Strength, psi | 39,900 | |||
Elongation | 55% | |||
Rockwell Hardness | B85 | |||
Chemistry | Iron (Fe) | 70% | ||
Carbon (C) | 0.15% max | |||
Chromium (Cr) | 18% | |||
Manganese (Mn) | 2% max | |||
Nickel (Ni) | 9% | |||
Phosphorus (P) | 0.045% max | |||
Sulphur (S) | 0.03% max | |||
Silicon (Si) | 1% max |
310 Stainless Steel
This alloy’s strength contains a mixture of its excellent strength and good corrosion resistance at temperatures in excess of 2100 degrees Fahrenheit (1149 C). And because of its higher chromium and nickel content, 316L stainless steel is preferred over 304 or 309 stainless in most applications.
It is widely used in boiler baffles, fireboxes, lead pots, kilns, radiant tubes, and oven linings.
310 Stainless Steel (annealed condition) | ||||
---|---|---|---|---|
Minimum Properties | Ultimate Tensile Strength, ps | 89,900 | ||
Yield Strength, psi | 45,000 | |||
Elongation | 45% | |||
Rockwell Hardness | B85 | |||
Chemistry | Iron (Fe) | 48 – 53% | ||
Carbon (C) | 0.25% | |||
Chromium (Cr) | 26% | |||
Manganese (Mn) | 2% | |||
Nickel (Ni) | 19 – 22% | |||
Phosphorus (P) | 0.045% max | |||
Sulphur (S) | 0.03% | |||
Silicon (Si) | 1.5% |
321 Stainless Steel
321 stainless steel is another unique steel. However, titanium is used to stabilize this material for use in weldments that are likely to experience severe corrosion. Although the absence of carbide precipitation is a significant issue here, an outstanding level of corrosion resistance is in many mediums. Hence, it is nontoxic to many organic and inorganic substances. Alloy 304 has comparable characteristics, but titanium presence reduces carbide precipitation, making machining simpler.
321 Stainless Steel (annealed condition) | ||||
---|---|---|---|---|
Minimum Properties | Ultimate Tensile Strength, ps | 89,900 | ||
Yield Strength, psi | 34,800 | |||
Elongation | 45% | |||
Rockwell Hardness | B80 | |||
Chemistry | Iron (Fe) | 68% | ||
Carbon (C) | 0.08% | |||
Chromium (Cr) | 18% | |||
Manganese (Mn) | 2% | |||
Nickel (Ni) | 11% | |||
Phosphorus (P) | 0.045% max | |||
Sulphur (S) | 0.03% | |||
Silicon (Si) | 1% | |||
Titanium (Ti) | 0.15% |
347 Stainless Steel
Similar to that of stainless steel type 321, type 347 employs columbium as a regulating element to make the most of its primary property, which is resilience to intergranular corrosion. It may be used in various applications that need frequent heating between 800 and 1650 F. (427-899 C). It performs admirably as high-temperature gaskets, chemical manufacturing apparatus, exhaust manifolds, expansion joints, rocket engine components, and aircraft collection rings.
347 Stainless Steel (annealed condition) | ||||
---|---|---|---|---|
Minimum Properties | Ultimate Tensile Strength, ps | 95,000 | ||
Yield Strength, psi | 39,900 | |||
Elongation | 45% | |||
Rockwell Hardness | B85 | |||
Chemistry | Iron (Fe) | 68% | ||
Carbon (C) | 0.08% max | |||
Chromium (Cr) | 17% | |||
Manganese (Mn) | 2% | |||
Nickel (Ni) | 11% | |||
Niobium (Nb) + Tantalum (Ta) | 0.8% | |||
Phosphorus (P) | 0.045% max | |||
Sulphur (S) | 0.03 | |||
Silicon (Si) | 1% |
410 Stainless Steel
This kind of stainless steel may be heat treated, and it finds widespread use in environments where corrosion is not extreme. Examples of applications include food acids, air, certain chemicals, and clean water. Many different things may be made from this material. The most common ones are turbine parts, bushings, flatware, and fasteners.
410 Stainless Steel (annealed condition) | ||||
---|---|---|---|---|
Minimum Properties | Ultimate Tensile Strength, ps | 65,000 | ||
Yield Strength, psi | 30,000 | |||
Elongation | 20 – 34 | |||
Rockwell Hardness | B82 | |||
Chemistry | Iron (Fe) | 86% | ||
Carbon (C) | 0.15% max | |||
Chromium (Cr) | 12.5% | |||
Manganese (Mn) | 1% max | |||
Phosphorus (P) | 0.04% max | |||
Sulphur (S) | 0.03% |
416 Stainless Steel
This is for use in natural food acids, basic salts, and water, as well as in most atmospheres.
416 Stainless Steel (annealed condition) | ||||
---|---|---|---|---|
Minimum Properties | Ultimate Tensile Strength, ps | 74,700 | ||
Yield Strength, psi | 39,900 | |||
Elongation | 30% | |||
Rockwell Hardness | B82 | |||
Chemistry | Iron (Fe) | 84% | ||
Carbon (C) | 0.15% max | |||
Chromium (Cr) | 13% | |||
Manganese (Mn) | 1.25% max | |||
Molybdenum (Mo) | 0.6% max | |||
Phosphorus (P) | 0.06% max | |||
Sulphur (S) | 0.15% min | |||
Silicon (Si) | 1% max |
430 Stainless Steel
Grade 430 stainless steel may also be referred to as the type 1.4016 designation. Corrosion-resistant Type 430 stainless steel has excellent formability and flexibility.
The quality of the finish on this ferritic, non-hardenable, plain chromium stainless steel is exceptional.
Grade 430 is resistant to nitric assault, making it a suitable choice for various chemical processes. For the most part, 430 is used in household appliances and ornamental moldings.
430 Stainless Steel (annealed condition) | ||||
---|---|---|---|---|
Minimum Properties | Ultimate Tensile Strength, ps | 75,000 | ||
Yield Strength, psi | 50,000 | |||
Elongation | 25% | |||
Rockwell Hardness | B85 | |||
Chemistry | Iron (Fe) | 87% | ||
Carbon (C) | 0.12% max | |||
Chromium (Cr) | 11% | |||
Manganese (Mn) | 1% max | |||
Phosphorus (P) | 0.04% max | |||
Sulphur (S) | 0.03% min | |||
Silicon (Si) | 1% max |
15-5 Stainless Steel
PH, or precipitation-hardening, stainless steel is a vacuum arc remelted grade. Aircraft manufacturers rely on this alloy partly for its high tensile strength and the variety of heat treatments available to tailor its hardness or other attributes to a specific need.
15-5 PH Stainless Steel Condition A (annealed) | ||||
---|---|---|---|---|
Minimum Properties | Ultimate Tensile Strength, ps | 161,000 | ||
Yield Strength, psi | 140,000 | |||
Elongation | 7.6% | |||
Rockwell Hardness | C35 | |||
Chemistry | Iron (Fe) | 71.91 – 79.85% | ||
Carbon (C) | 0.07% max | |||
Chromium (Cr) | 14 – 15.5% | |||
Manganese (Mn) | 1% max | |||
Niobium (Nb) + Tantalum (Ta) | 0.15 – 0.45% ma | |||
Nickel (Ni) | 3.5 – 5.5% | |||
Phosphorus (P) | 0.04% max | |||
Sulphur (S) | 0.03% min | |||
Silicon (Si) | 1% max |
17-4 Stainless Steel
This kind of stainless steel is also known as a PH grade, which stands for precipitation-hardening. Much as with 304, this alloy is often used in airplanes because of its tensile purity and the variety of heat treatments available to achieve desired hardness or other qualities. Like 15-5, 17-4 has a similar composition but is somewhat more magnetic due to its higher ferrite concentration.
17-4 PH Stainless Steel Condition A (annealed) | ||||
---|---|---|---|---|
Minimum Properties | Ultimate Tensile Strength, ps | 160,000 | ||
Yield Strength, psi | 145,000 | |||
Elongation | 5% | |||
Rockwell Hardness | C35 | |||
Chemistry | Iron (Fe) | 69.91 – 78.85% | ||
Carbon (C) | 0.07% max | |||
Chromium (Cr) | 15 – 17.5% | |||
Manganese (Mn) | 1% max | |||
Niobium (Nb) + Tantalum (Ta) | 0.15 – 0.45% max | |||
Nickel (Ni) | 3 – 5% | |||
Phosphorus (P) | 0.04% max | |||
Sulphur (S) | 0.03% min | |||
Silicon (Si) | 1% max |
17-7 Stainless Steel
This is chrome-nickel stainless steel with high strength, moderate corrosion resistance, and qualities suitable for flat springs. It applies to temperatures up to and including 800 degrees Fahrenheit in service, where high strength, corrosion resistance, and mechanical qualities are needed. As a result of its low level of distortion when subjected to heat treatment, it is often used to produce exceedingly complex and complicated components. It is very steady. Many different types of springs and washers include this substance.
17-7 PH Stainless Steel Condition A (annealed) | ||||
---|---|---|---|---|
Minimum Properties | Ultimate Tensile Strength, ps | 130,000 | ||
Yield Strength, psi | 40,000 | |||
Elongation | 35% | |||
Rockwell Hardness | B85 | |||
Chemistry | Iron (Fe) | 70.59 – 76.75% | ||
Carbon (C) | 0.09% max | |||
Chromium (Cr) | 16 – 18% | |||
Aluminum (Al) | 0.75 – 1.5% max | |||
Manganese (Mn) | 1% max | |||
Nickel (Ni) | 6.5 – 7.75% | |||
Phosphorus (P) | 0.04% max | |||
Sulphur (S) | 0.03% min | |||
Silicon (Si) | 1% max |
Nitronic 50 Stainless
This nitrate-enhanced austenitic stainless steel delivers corrosion resistance and strength in one material. It has an enhanced corrosion resistance compared to T316 and T316L, in addition to almost double the yield strength of those two alloys. This, of course, makes it an excellent mechanical quality at both high and very freezing temperatures.
Nitronic 50 Stainless Steel (annealed condition) | ||||
---|---|---|---|---|
Minimum Properties | Ultimate Tensile Strength, ps | 116,000 | ||
Yield Strength, psi | 57,000 | |||
Elongation | 47% | |||
Rockwell Hardness | B91 | |||
Chemistry | Iron (Fe) | 58% | ||
Chromium (Cr) | 22% | |||
Manganese (Mn) | 5% | |||
Molybdenum (Mo) | 2.25% | |||
Nitrogen (N) | 0.3% | |||
Nickel (Ni) | 12.5% | |||
Silicon (Si) | 1% max |
Nitronic 60 Stainless
It has outstanding resistance to galling as well as corrosion. Additionally, it has double the yield stress as T304. There also has excellent resistance to metal-on-metal abrasive wear.
Nitronic 60 Stainless Steel (annealed condition) | ||||
---|---|---|---|---|
Minimum Properties | Ultimate Tensile Strength, ps | 103,000 | ||
Yield Strength, psi | 60,000 | |||
Elongation | 64% | |||
Rockwell Hardness | B95 | |||
Chemistry | Iron (Fe) | 62% | ||
Chromium (Cr) | 17% | |||
Manganese (Mn) | 8% | |||
Nitrogen (N) | 0.14% | |||
Nickel (Ni) | 8.5% | |||
Silicon (Si) | 4% max |
Request for Quotation
Request For Quote
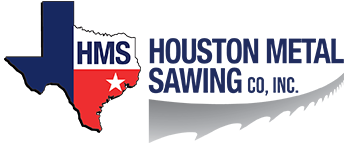
Monday through Friday
8:00 AM to 5:00 PM Central Time
Houston, Texas 77093
Our sawing capabilities include a large range of metals, castings, plastics or molded parts. You can count on Houston Metal Sawing to deliver your parts on time and within budget.
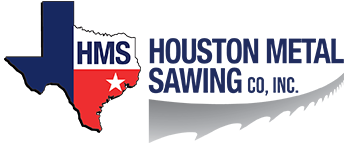